KAUFFMANN bedding combines the passion for refined down and feathers with a love of detail – in top quality which is unique worldwide.
Down in fine fabric
For the covers we use our finest Bramscher Tuch fabric. These are particularly breathable, soft and high-quality fabrics. because deep, regenerative sleep is part of a fulfilled existence – and worth all the effort! We are proud of every duvet which leaves our premises.
And so every duvet that leaves our premises fills us with pride. After all, we still process and refine our down today with the same passion as displayed by the founders of our company.
Innovation since 1885
Consumers long for constant improvement of their own living environment and are therefore willing to invest in it. We have recognised this trend. Based on our 130 years of experience, we develop and research with the claim: “Only those who are always at the forefront can determine the direction”. With this goal in mind, we create fine thread fabrics of the highest quality.
|
|
|
The fabric
After weaving, a cloth is a raw material in the truest sense of the word. Innovative finishing techniques are needed to turn it into a fine, soft and breathable Künsemüller bed shells. At this point, our expertise is required to produce down-proof fabrics with an excellent moisture transfer, a lovely softness and the perfect feel. In addition, we process exquisitely refined fabrics such as the “Bramscher Tuch”.
|
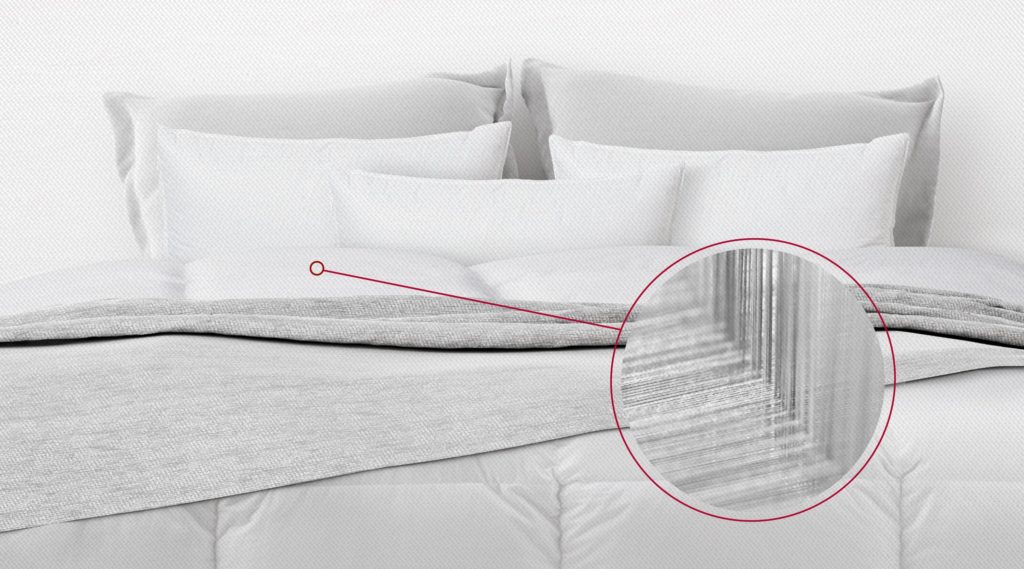
Thread count
Is calculated by adding the number of threads in both directions oft he wave – the warp and the weft, either in centimetres or inches. If a multi thread yarn is used for weaving, the threads count. All the casings we use have sufficiently high thread counts. Thus we not only prevent down and feathers escaping, but also stop the smallest dust mite from penetrating the casing.
|
|
|
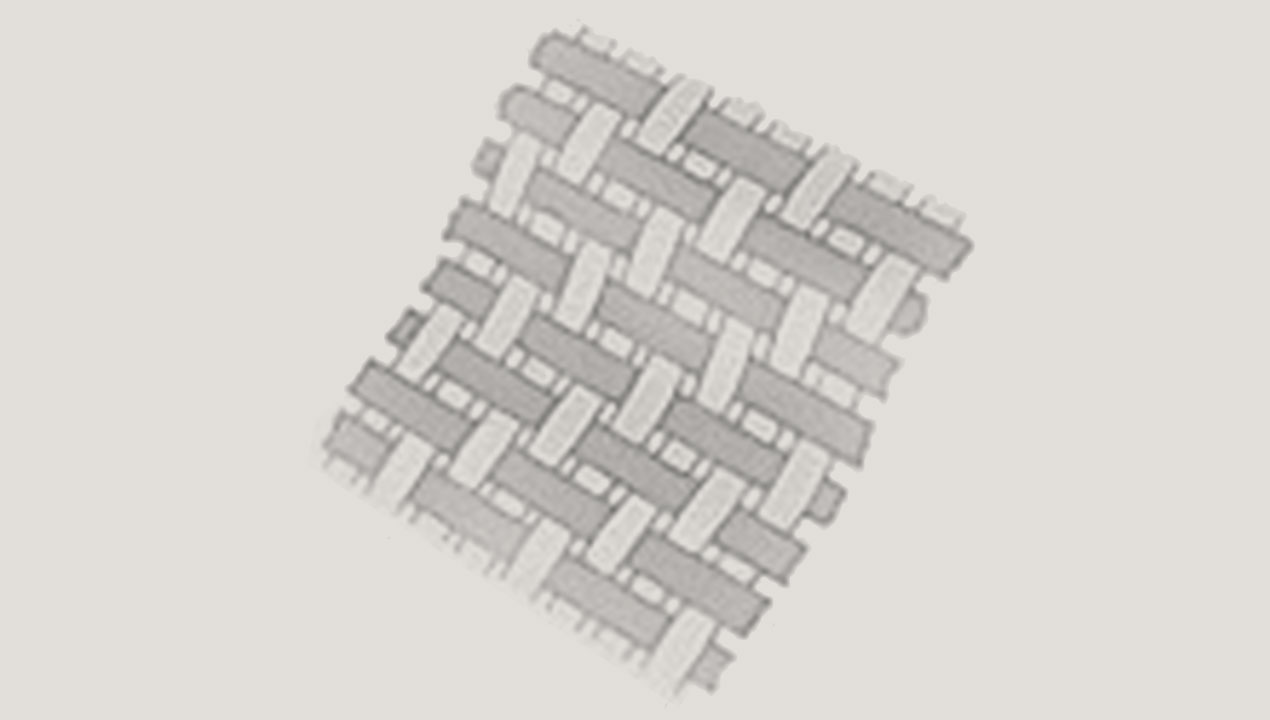
TICKING
he twill weave, which could be described as the original of ticking weaving, has a high degree of durability due to its high thread density. At the same time, it impresses with its extreme suppleness. Woven fabrics in twill weave can usually be recognized at one glance because of their diagonal twill ridges. The ridges result from the diagonal offset of the weave points. Each warp thread lies once above and twice below the individual weft threads – the best basis for feather- and down-tight pillow and duvet shells.
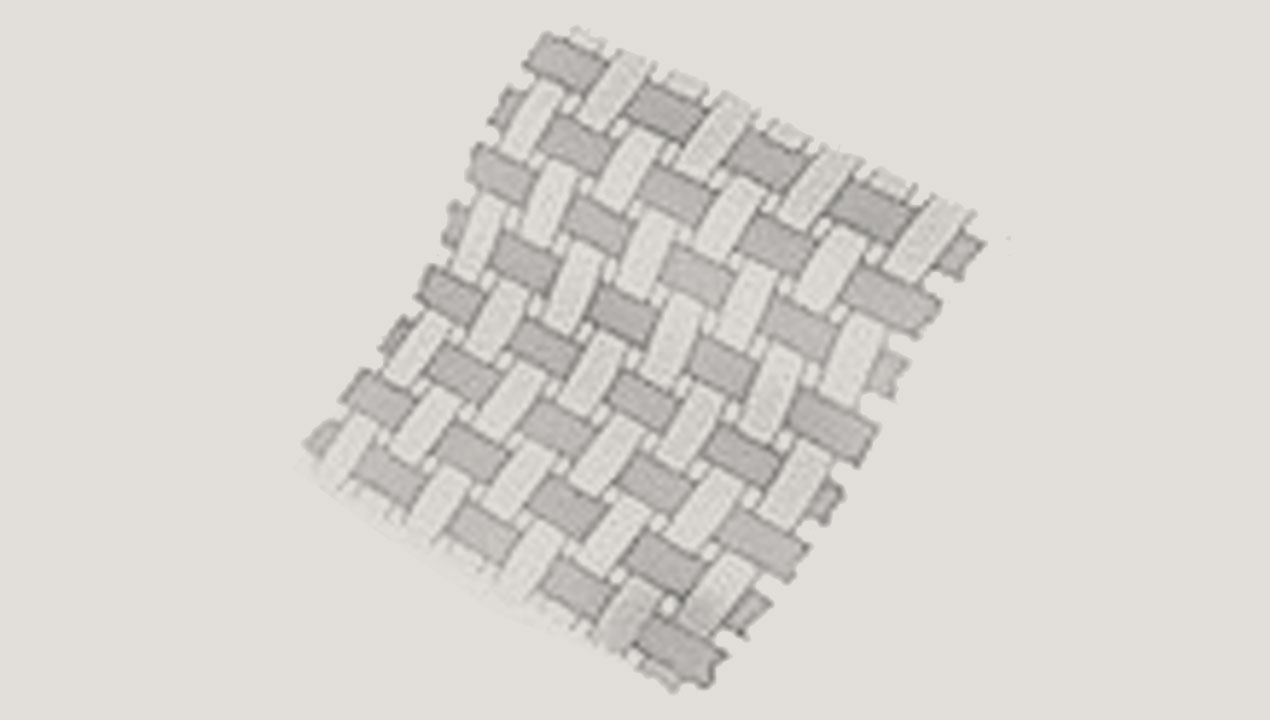
Cambric
They are recognised by their frequent crossing points. By weaving the finest cotton yarns, the fabric pores are kept so small that the down cannot penetrate them. The simplest and at the same time closest crossing of warp and weft threads: each warp thread lies alternately once above and once below the individual weft threads.
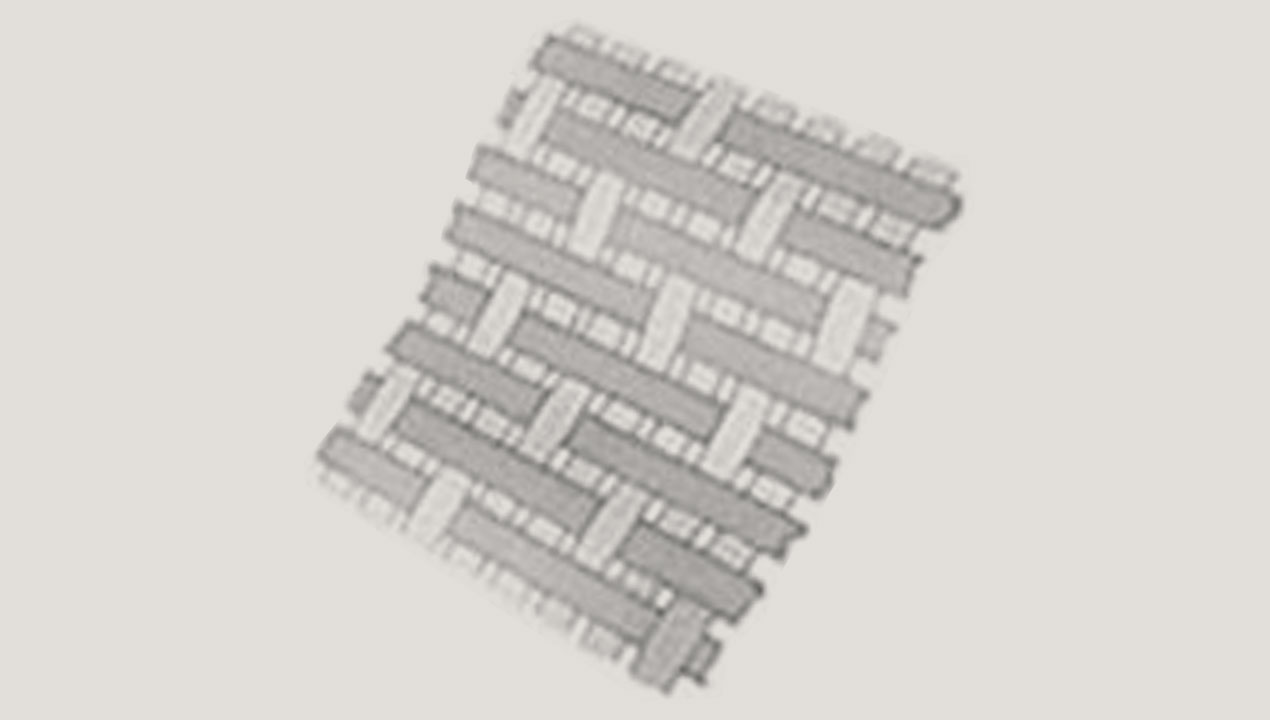
Sateen
Atlas bindings are usually easily recognised by their smooth surfaces that do not seem to have a structure and their silky sheen. Both is achieved through the evenly distributed crossing points. When combined with high-quality fillings you create particularly fine bedding.
REFINEMENT
After weaving, a cloth is a raw material in the truest sense of the word. Innovative finishing techniques are needed to turn it into a fine, soft and breathable Künsemüller bed shells. At this point, our expertise is required to produce down-proof fabrics with an excellent moisture transfer, a lovely softness and the perfect feel. In addition, we process exquisitely refined fabrics such as the “Bramscher Tuch”.
|
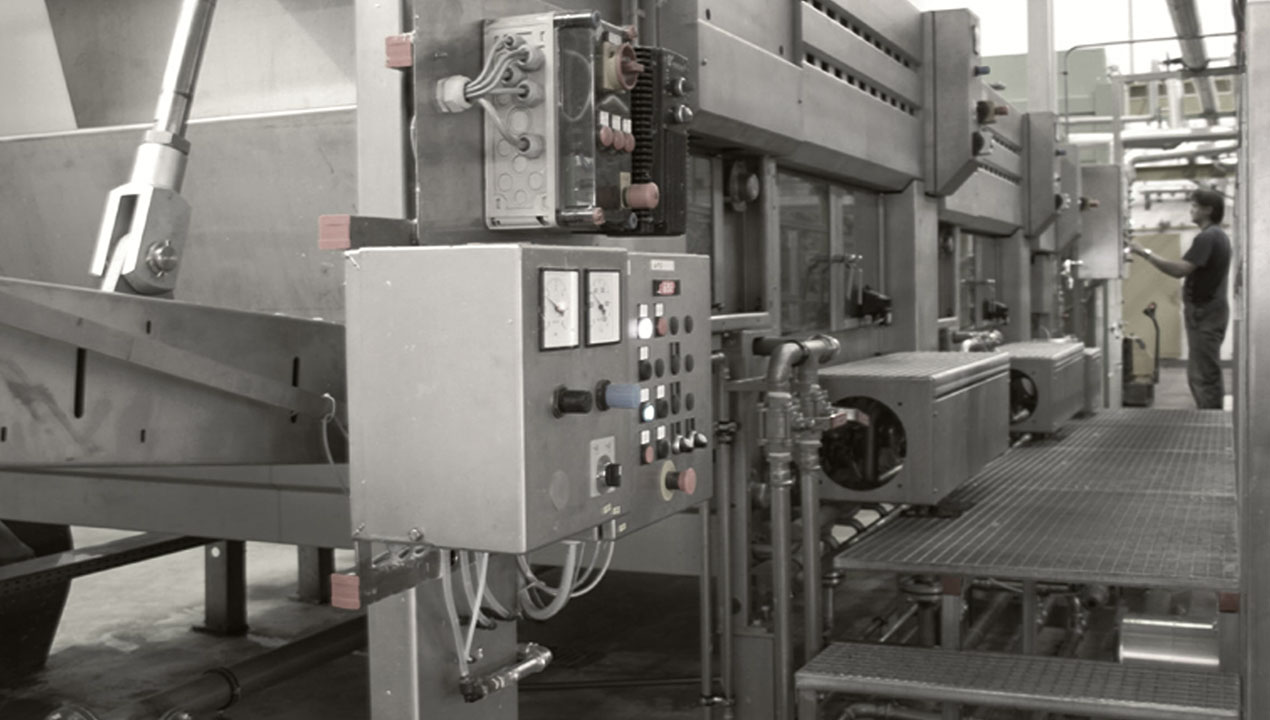
Singeig & Desizing
In order to remove the protruding fibres from a fabric, it is singed, ie. the fine hairs are burnt off. This only happens on the right side of the fabric, which is visible later.
During the ensuing desizing phase the sizing agent is dissolved so that it can be washed out.
(The purpose of the sizing is to increase the resistance of the warp threads).
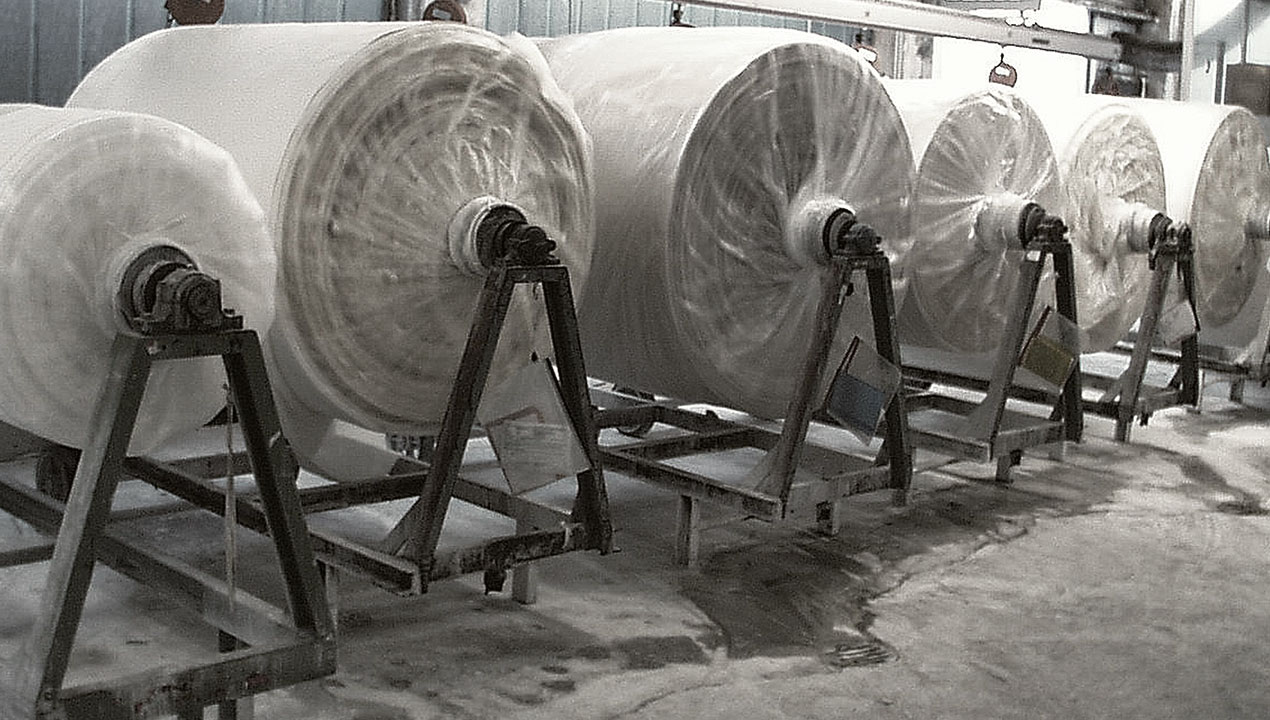
Bleaching & Dwelling
White cotton fibres also show natural yellowing, which is removed with an oxidative bleaching agent. We use hydrogen peroxide which has to react and dwell for 48 hours.
After this time, the fabric is washed again, because only white bedding and bedding for medical applications have the highest level of cleanliness and absorption.
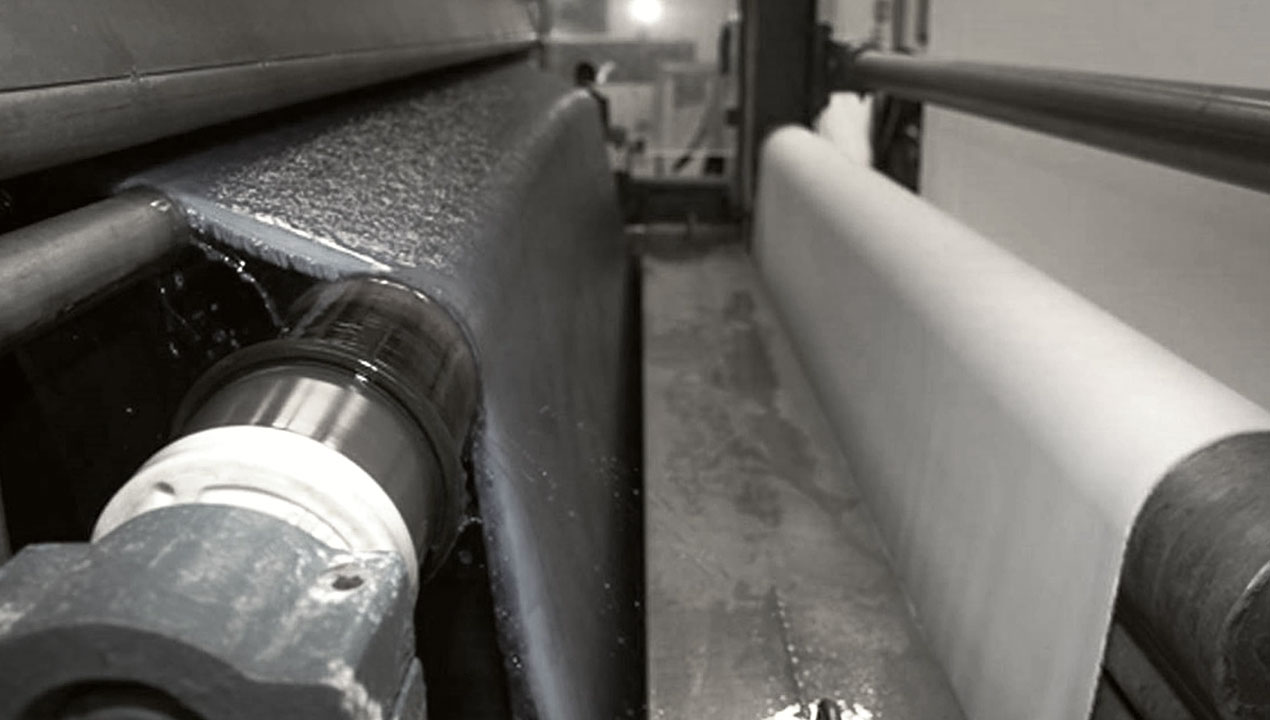
Dyeing & Drying
Dyeing involves applying a reactive dye to the fabric, which forms a chemical bond with the fibre. After a pre-set dwell time, the fabric is washed again to remove unbound dye.
The fabric is then dried on the stenter frame and stretched to the appropriate width.
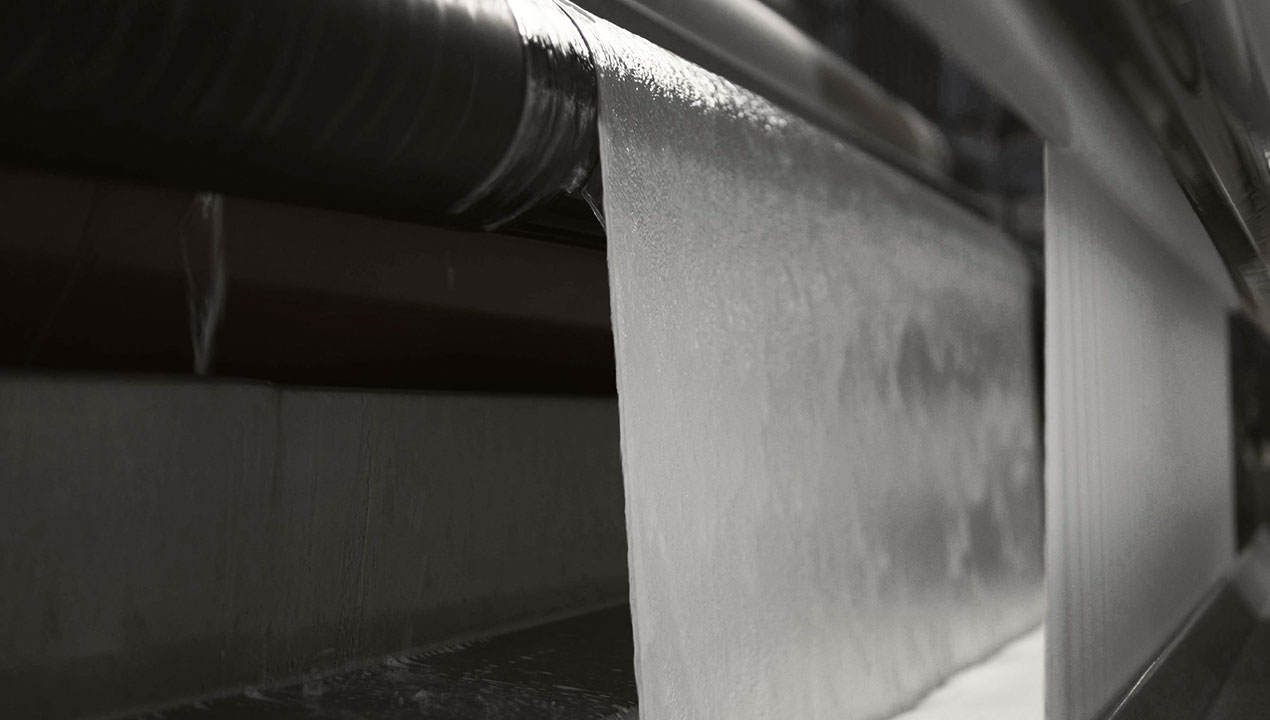
Finishing
During the finishing process the fabric is made soft and supple in order to give the fabric the optimum feel.
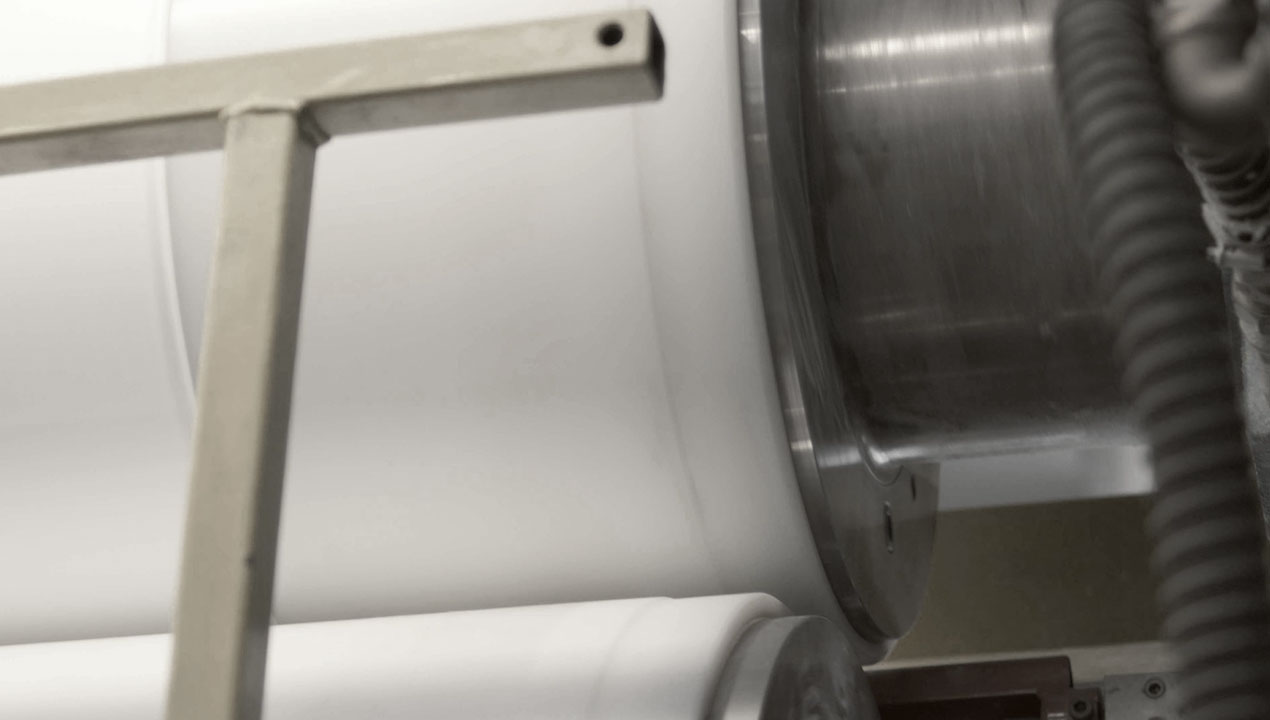
Calendering & Shrinking
In the calendering process the fabric is passed under pressure between rolls that make the fabric smoother and denser. Both pressure and speed influence the texture of a fabric.
To prevent shrinkage of the fabric, the fabric is pre-shrunk by mechanically compressing the fabric with a rubber blanket. At the same time, it gives the fabric a more supple and softer feel.